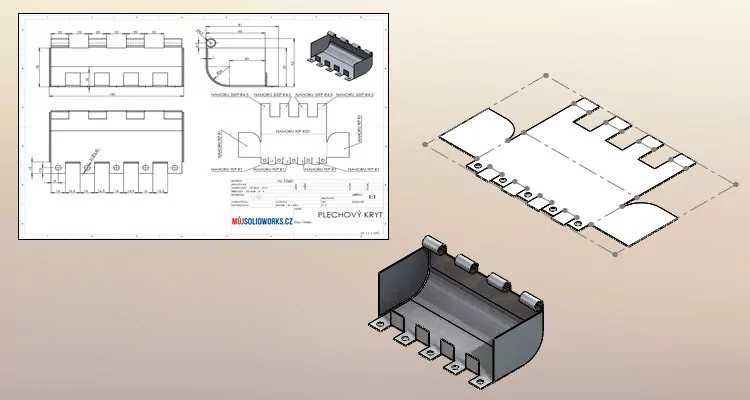
Konstrukce plechových dílů vychází z teoretických a praktických zkušeností konstruktéra. Pouze zkušený konstruktér, který má povědomí o technologii výroby a zpracování plechových dílů, může navrhnout správný model plechu, který je vyrobitelný s ohledem na dostupnou infrastrukturu firmy (strojový park) a požadované funkční a mechanické vlastnosti dílu. V tomto díle seriálu Výroba plechových dílů vám představíme, jak se vyrábí a zpracovávají plechové díly.
Tip: Seriál Výroba plechových dílů obsahuje témata, která jsou velice často vyhledávána uživateli SOLIDWORKSu. Podívejte se sami na další obsah seriálu, který jsme pro vás připravili s ohledem na konstrukci plechových dílů v SOLIDWORKSu.
Technologie výroby plechů
Plech je hutní polotovar (kovová deska), který se vyrábí tvářením (kováním, tažením nebo válcováním) za tepla a za studena v různých tloušťkách a rozměrech, které jsou normalizovány. Tabule plechu slouží jako polotovar pro další zpracování a její výroba je znázorněna a popsána ve videu:
Konstruktér volí velikost tabule plechu podle rozměrů plechového dílu v rozvinutém tvaru. Konstruktér tak získá tzv. nástřihový plán, který souvisí s efektivitou využití materiálu z celé tabule plechu. Hospodárné využití plechu by mělo být co nejvyšší a odvíjí se od geometrie plechu v rozvinutém tvaru a jeho uspořádání na tabuli plechu. Jakmile je dělením získán rozvinutý tvar plechu z tabule plechu, dokončuje se jeho finální tvar ohýbáním (ohraňováním) a post-procesními úpravami (třískové obrábění, tepelné zpracování a povrchové úpravy).
Technologie zpracování plechů
Výrobu plechu z hutního polotovaru (tabule plechu) lze rozdělit do tří výrobních etap:
- příprava polotovaru plechu v rozvinutém tvaru (stříhání, řezání),
- tvarování plechu do ohnutého tvaru (ohýbání, skružování, lisování),
- postprocesní úpravy (obrábění přesných otvorů, svařování, tepelné zpracování, povrchové úpravy).
Rozvinutý tvar plechu lze z tabule plechu získat:
- mechanickým řezáním (pásová pila, kotoučová pila apod.),
- stříháním (vystřihováním),
- řezáním vysokým zdrojem energie (plamenem, plazmou, laserem, vodním paprskem).
Mechanické řezání
Mechanickým řezáním je myšleno oddělování třísek základního materiálu nástrojem (řezný nástroj), který je tvrdší než řezaný materiál. Nejčastěji se používá pilový list nebo pilový kotouč.
Dělení materiálu kotoučovou pilou pod daným úhlem:
Stříhání
Stříhání plechů je nejrozšířenější metodou výroby pro finální výrobek nebo pro polotovar určený k dalšímu zpracování. V praxi se používá z důvodu nízké cenové náročnosti. Podstatou stříhání je oddělování materiálu protilehlými břity nožů, přičemž oddělení nenastane přesně v žádné rovině. K tomuto jevu dochází proto, že je materiál elastický, tvárný a smykové napětí způsobuje tlak nožů na celé ploše. Zpravidla jsou střižné hrany deformovány plochou nástroje, proto vyžadují další opracování. Stříhání se provádí zastudena a v případě málo plastických ocelí se využívá předehřevu (250 až 400 °C). Na kvalitu střižného procesu má rozhodující vliv střižná mezera mezi noži. Velikost střižné mezery závisí nejen na mechanických vlastnostech stříhaného materiálu, ale také na jeho tloušťce.
Stříhání plechu je znázorněno ve videu:
Řezání plamenem
Řezání plamenem se zpravidla používá pro dělení materiálu a jedná se o proces, kdy dochází k ohřátí materiálu na teplotu, při které dojde k chemické reakci – hoření (cca 1200 °C). Pro řezání se používá směs kyslíku a acetylenu. V praxi se řezání plamenem používá pro materiály o tloušťce 3 a 300 mm.
Řezání plechů plamenem je znázorněno ve videu:
Řezání plazmou
Při řezání plazmou je základní materiál postupně odtavován a odpařován paprskem plazmy, vystupujícím vysokou rychlostí z plazmového hořáku. Plazma je směs volných elektronů, pozitivně nabitých neutrálních atomů o vysoké teplotě (10 až 30 tisíc °C). Tryska plazmy je chlazena kolující vodou, a při některých procesech se dokonce řezný materiál umisťuje pod vodu. Voda chrání trysku před roztečením, brání hluku a nepříjemnému dýmu. Složení plynu se odvíjí podle použití a nejčastěji se volí argon, dusík, vodík, kyslík a jejich směsi.
Řezání plechu plazmou:
Řezání laserem
Princip řezání laserem spočívá v odebrání základního materiálu pomocé úzkého paprsku monochromatického světla, soustředěného na velmi malou plochu. V místě dopadu paprsku dochází k přeměně světelného záření na tepelnou energii o hustotě řádově až 108 W·mm-2. V místě řezu je teplota okolo 10 tisíc °C, čímž dochází k odtavení nebo odpaření materiálu v místě řezu. Technologie je cenově nákladnější, s ohledem na kvalitu povrchu v porovnání s řezáním plynem nebo plazmou se volí ve strojírenské praxi častěji.
Řezání plechu laserem:
https://www.youtube.com/watch?v=SG8h1Ykf1lc
Řezání vodním paprskem
Princip řezání vodním paprskem spočívá v odbrušování základního materiálu abrazivem, které jé unášeno kapalinou. Základem řezacího stroje je vysokotlaké čerpadlo a multiplikátor. Pomocí nich generuje tlak až 400 MPa (4 tisíce barů), který je přiváděn potrubím k řezací hlavě. V řezací hlavě je směšovací komora, kde proud kapaliny o vysokém tlaku a rychlosti strhává abrazivo. Takto vytvořený paprsek dopadá na řezaný materiál, kde jej zrnka abraziva s velkou kinetickou energií vybrušují. Výhodou vodního paprsku je to, že oblast řezu není teplotně ovlivňována a tato teplota se pohybuje okolo 40 °C. Vysokou přidanou hodnotu vodního paprsku je možnost řezání jakýchkoliv materiálů, včetně nevodivých. Nevýhodou je styk s vodou a poměrně vysoká cena provozu.
Řezání vodním paprskem:
Ohýbání (ohraňování)
Ohýbání je operace, která se zpravidla provádí za studena. Při ohybu dochází k elasticko-plastické deformaci ohýbaného materiálu a na velikost deformace má vliv jakost materiálu, tloušťka v místě ohybu a směr vláken materiálu. Orientace vláken v materiálu, vzniklých při výrobě, je rozhodující pro životnost a únosnost ohýbané součásti. Osy ohybu by měla být kolmá na směr vláken materiálu nebo minimálně pod úhlem 30°. Charakteristickým znakem při ohýbání je změna tvaru plochy ohybu. Při ohýbán polotovarů užších se příčný průřez mění daleko víc než u širokých. Při ohybu širokých polotovarů dochází k zeslabení tloušťky, ale příčný průřez se téměř nemění. Při ohybu působí v příčném průřezu ohybové a tlakové napětí. V místě neutrální osy se nachází beznapěťový stav, což je přechod tahového a tlakového napětí. Tato osa je důležitá pro výpočet výchozí délky polotovaru. Pro ohýbání je typické odpružení ohnuté části. Při ohýbání musíme vynaložit sílu na překonání pružné a následně plastické deformace. Po odlehčení zatěžující síly plastické deformace zůstanou a pružné deformace se vrátí. Proto se v praxi musí plech ohnout o požadovaný úhel a úhel odpružení.
Přesné ohýbání plechu na ohraňovacím lise Trumpf TruBend 7036:
Stejně jako lze simulovat obrábění v CAM aplikacích, můžeme simulovat proces ohýbání plechu a předejít tak výrobním chybám:
Skružování
Skružováním se připravují plechy kruhových tvarů. Ty bývají zpravidla částmi tlakových nádob, ať už jsou kruhové nebo kuželové. Tato technologie vychází z pohybu rotujících válců, kde spodní válec slouží jako podpěra a horní válec se postupně přitlačuje a vytváří skruž. Skružovačky mohou být tří nebo čtyřválcové. Skružování je ve strojírenské praxi velmi často používáno jako přípravná operace pro svařování.
Ukázka automatického zakružování plechu:
Svařování
Svařování je jednou z velmi používaných výrobních operací u plechových dílů a metoda svařování se volí podle výrobních specifikací, druhu materiálu a požadavků na výrobu.
Třískové obrábění
Třískové obrábění se používá zejména pro výrobu menších součástí, jako jsou návarky, rotační části nádob anebo pro vrtání (vystružování) přesných otvorů. Vrtání otvorů může být provedeno před montáží nebo pro získání přesných otvorů až po montáži nebo svaření. Pro třískové obrábění se používá celá řada řezných nástrojů a spolehlivých řezných materiálů a zpravidla se provádí na CNC obráběcích strojích. S ohledem na problematiku vrtání do plechu se používají speciální stupňovité vrtáky a korunkové vrtáky, které vyvrtají díru spolehlivě i bez vyosení nástroje z místa řezu nebo znehodnocení plechu. Pro získání kvalitního povrchu se používají optimální řezné parametry, které se odvíjí od obráběného materiálu. S volbou nástrojů a nastavením řezných podmínek pomáhají dodavatelé řezných nástrojů.
Ukázka vrtání do plechu korunkovým vrtákem:
Tepelné zpracování
Během svařování dochází k tepelnému ovlivnění v oblasti svaru a zejména v oblastech, kde je vysoká koncentrace svarových spojů na jednom místě. Snížit vnitřní napětí lze tepelným zpracováním s charakteristickým technologickým průběhem, který se skládá z ohřevu na patřičnou teplotu, výdrží na této teplotě a řízeném ochlazování. To probíhá pozvolna a následně na vzduchu. Průběh žíhání se odvíjí od materiálu plechu.
Povrchové úpravy
Nejčastější využití v praxi nachází plechy z oceli se základní povrchovou úpravou, kterou je odmaštění nebo chemická předúprava. Dále se můžete setkat s plechy měděnými, mosaznými, hliníkovými, ošetřenými povrchovou úpravou (např. pozinkování okapů a svodů vody ze střechy domů) nebo s nanesenou vrstvou organického povlaku (na bázi akrylátů, polyvinyldendifluoridu – viz obr. níže, polyesterů, epoxidů, polyuretanů a dalších specifických pryskyřic).
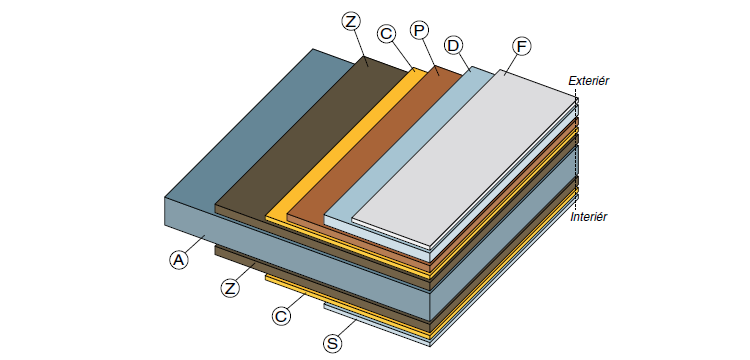
A – plech v kvalitě oceli S320 a speciální povrchová úprava pro vnější a vnitřní použití
odolná proti povětrnostním a chemickým vlivům
Z – vrstva zinku 200–275 g·m-2
C – chemické opracování
S – rubová strana ochranný lak 5–10 µm
D – polyvinylidén-fluoridový lak 18–25 µm
F – odstranitelná fólie
P – základový lak 3–5 µm
Úprava povrchu zabraňuje opotřebení, vzniku korozi, zvyšuje odolnost vůči vysokým teplotám a agresivnímu prostředí, vzdoruje naleptání, odolává UV záření a křídování a prodlužuje životnost plechu. Mezi další povrchové úpravy plechů patří kartáčování (řízená textura plechu), broušení, barvení a lakování.
Komentáře k článku (0)
Přidávat komentáře k článku mohou pouze přihlášení uživatelé.
Chcete-li okomentovat tento článek, přihlaste se nebo se zaregistrujte.